Part 2: Expanding Shipping Temperatures Without Sacrificing Quality: A Guide to Transport Validation and PQ
Demonstrating Product Quality All pharmaceutical manufacturers must ensure that the safety and efficacy of...
read Details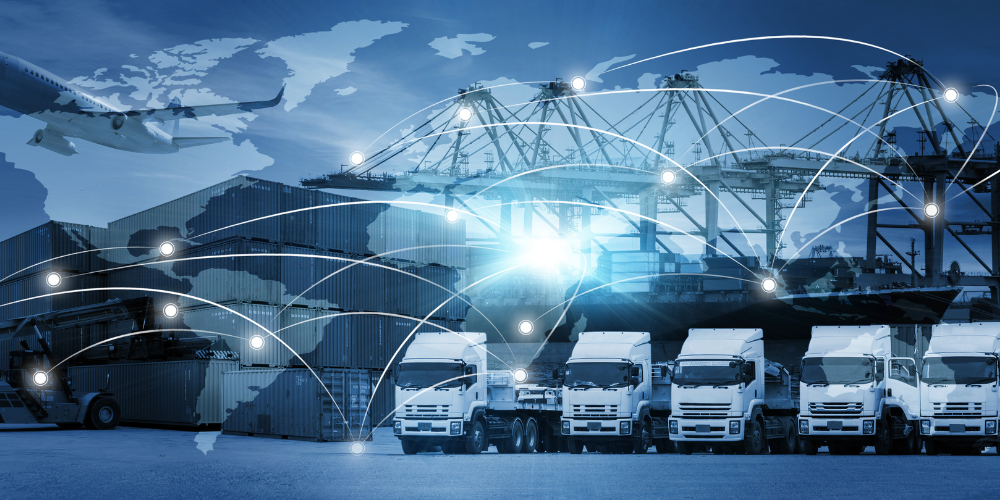
First published on May 11, 2015 on Cold Chain IQ – as a contributor, Hutchinson’s column, Global Cold Chain Connections, falls in the Supply Chain & Security category. Join Cold Chain IQ today to access informative cold chain articles.
By Gary Hutchinson
A drug can take a variety of paths from the manufacturer to the patient. Most often, the product leaves the manufacturer’s direct control and enters a complex system of handoffs (see chart from US Pharmacopoeia). Distribution systems that deliver pharmaceutical products require special handling based on the conditions clearly indicated in the labeling for the product. The Prescription Drug Marketing Act of 1987 and the ensuing regulations in 21 CFR Part 203, Prescription Drug Marketing, and Part 205, Guidelines for State Licensing of Wholesale Prescription Drug Distributors, provide the necessary regulations and guidance for several legs of the distribution chain for the prescription drug.
Manufacturers are obligated to include distribution as part of their overall quality system and should be continuously monitored and updated to adhere to industry best practices. Current Good Distribution Practices (cGDPs) for the pharmaceutical supply chain have been divided into seven different categories (Stability, Distribution Control Management, Performance Management, Supply Chain Partner Management, Qualification / Validation, Continuous Improvement, and Import / Export Compliance) in PDA Technical Report #52.
Distribution Control Management in a comprehensive cGDP quality system covers the logistics management for final drug product in four key ways:
• Qualifications and training of personnel
• Facilities, material handling, and storage and inventory control
• Non-conformance or exceptions, returns, and product disposition
• Transportation, third-party distribution, and product protection
Maintaining the cGDP quality system for transportation, third-party distribution, and product protection is a difficult challenge because of the distributed nature and contracted third-party relationships found across most modern controlled-environment logistics networks.
Coupled with the increased focus on high-growth protein products that are environmentally sensitive, the concerns during transportation are heightened for several reasons:
• Risk of introduction of adulterated and/or counterfeit product and product diversion
• Variances in equipment, facilities, skills, and experience across locations
• Significant and cumulative hazards to product quality — temperature with shock, vibration, pressure and humidity
Pharmaceutical products are the most vulnerable during transport. Managing supply chain security risks during transport is important to mitigate the potential loss of revenue and reputation for manufacturers, distributors, and logistics providers. Training to detect and deter potential adulteration or diversion of drug product is needed.
Variances in equipment, material handling, personnel skills, and experience in handling pharmaceuticals for in-transit drug products are important to consider when preparing a validation master plan. These variances make the process validation of the controlled-environment logistics network at a high degree confidence (greater than 95%) difficult, especially when transporting protein-based products. Additional in-transit monitoring, procedural controls, visual indicators, and most importantly stability testing for distribution becomes necessary since validating to a high confidence interval is difficult to achieve.
Stability testing outlined in the ICH guidelines primarily addresses the establishment of expiry dating and storage conditions. The potential product impact in the distribution environment is not addressed. Shock and vibration testing have a role, particularly in the transportation of solution formulations of certain large proteins. Stability testing for distribution is needed: these tests are ‘dynamic’ when compared to current ‘static’ testing per ICH guidelines and should be designed to understand the cumulative and significant hazards to drug quality during transport.
Temperature-sensitive product may exceed long-term storage conditions established by the manufacturer at any time during manufacturing, distribution, and customer handling steps. The allowable time and temperature exposure to ranges outside of the long-term storage conditions for manufacturing is currently justified by using accelerated stability data gathered during static stability studies conducted under ICH guidelines.
However, these accelerated registration (or static) stability studies may be inadequate for the transport process, especially when dealing with protein formulations in solution. The accelerated studies are normally terminated without returning samples of the exposed product to normal storage conditions and conducting assay testing to the end of shelf life to confirm product. The cumulative effects of other environmental hazards on product outside long-term storage recommendations are essentially unknown with standard static stability studies as recommended under ICH guidelines. A gap in understanding exists on protein in solution formulation behavior after exposure to significant and cumulative hazards during transport. This gap should be a cause for concern.
One of the biggest risks to drug product in a controlled-logistics network is the freezing of final drug product. Even the temporary storage of a thermal packaging system into forced-air refrigeration cooler within its qualification time period will most likely cause low temperature exposures and potential freezing. Proper testing of drug products in freeze-thaw conditions for distribution is critical. Most freeze-thaw stability testing does not consider the effect of ‘supercooling’ on solutions.
The suppression of the freeze point or ‘supercooling’ and subsequent ‘flash’ freezing in current freeze-thaw stability testing guarantees a homogenous solid is formed. In the distribution environment, the vibration and shock events inherent in the logistics network practically guarantees freezing of a solution at its freezing point. The frozen solution is rarely homogenous and can be observed as slurry of frozen and liquid solutions. These conditions are detrimental to proteins in solutions because of the risk of increased protein concentration, and how it can cause protein denaturation, aggregation, degradation or inactivation. These conditions are not properly tested by current static stability studies.
The transport of final drug products is one the most difficult tasks in the pharmaceutical supply chain because of the sensitive nature of the product and the complexity in a modern logistics network. An integrated process management and product characterization approach using dynamic stability testing for distribution is required to minimize risks to drug product quality during transport.
The risks of not taking an integrated process management or conducting dynamic studies on final drug products can lead to significant compliance and business issues:
• Supply chain security measures across global and contracted third-party logistics networks are required to ensure protection against adulterated and/or counterfeit product and product diversion.
• The confidence interval possible during process validation of complex and highly variable controlled-environment logistics network require either robust product testing specifically for distribution or a significant increase in monitoring and controls and flexibility.
• The environmental hazards in the logistics network and potential impact to product quality at end of shelf life may not be adequately covered in the current product testing approach.
Any cGDP quality system focused on the controlled-environment logistics network will be continually challenged by non-conformances and exception management. This is a characteristic of a modern pharmaceutical logistics network. Dynamic stability testing of the final drug product specifically for distribution is a prerequisite in the development of a modern, world-class pharmaceutical supply chain.
Click here to view online
Demonstrating Product Quality All pharmaceutical manufacturers must ensure that the safety and efficacy of...
read DetailsIntroduction The integrity of supply chain management is pivotal in the demanding realm of...
read DetailsEntering the U.S. market comes with a unique set of regulatory challenges, particularly when...
read Details